Cable processing: cutting, soldering, crimping and laser stripping
With the reassurance of vast experience, rmw Kabelsysteme GmbH will create high-quality products out of first-class raw cable material and with the most modern technology. In this way, rmw works with you to realise exactly the cable configurations you need for your project.
Cable cutting
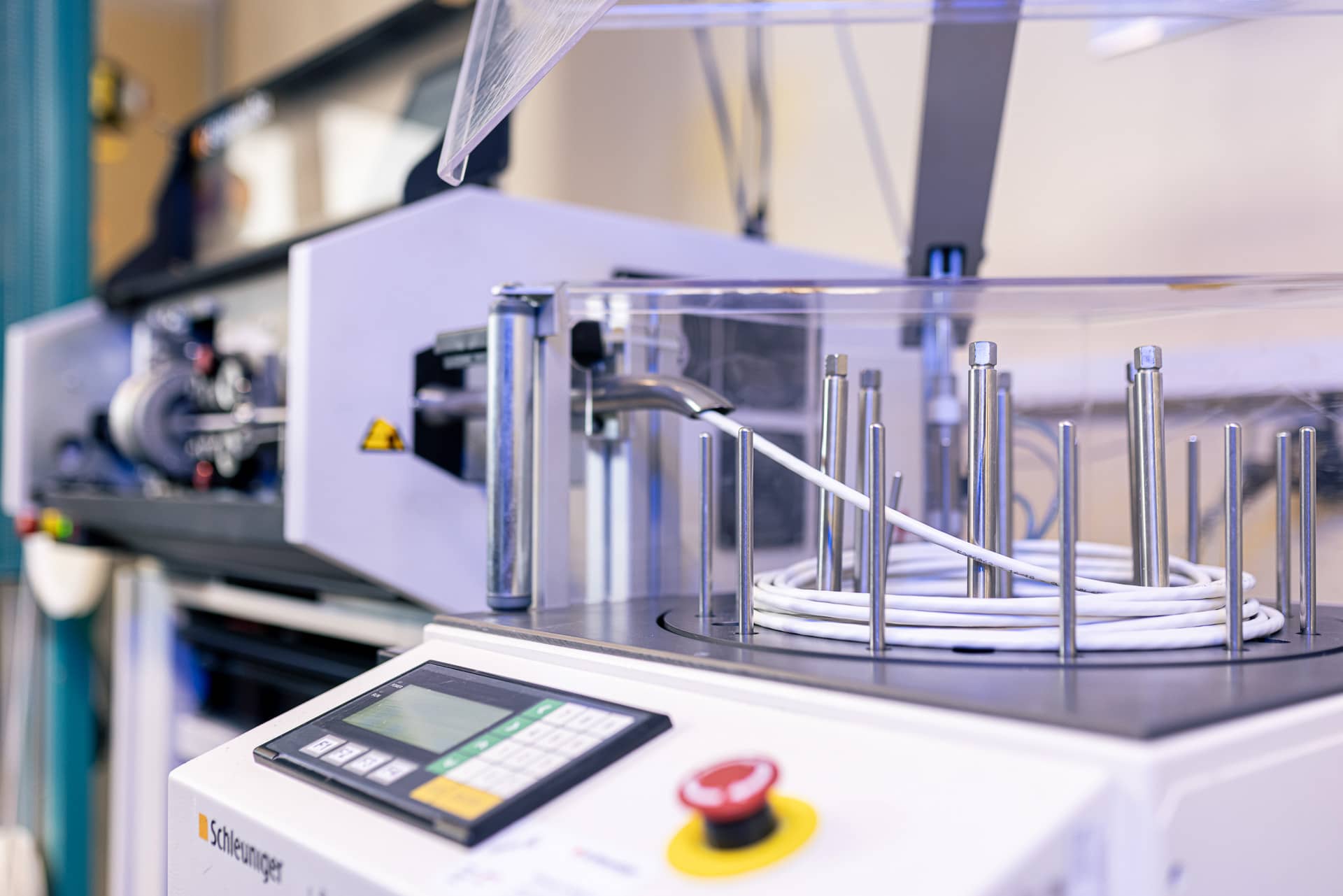
From a few millimetres to several hundred metres, up to 16 mm in diameter and beyond – all types of cables and shielding are processed and customised by rmw to meet the demands of your project. rmw's machinery is ideally equipped for this, including modern semi-automatic cutting and stripping machines as well as high-precision laser technology for sheath processing.
Soldering
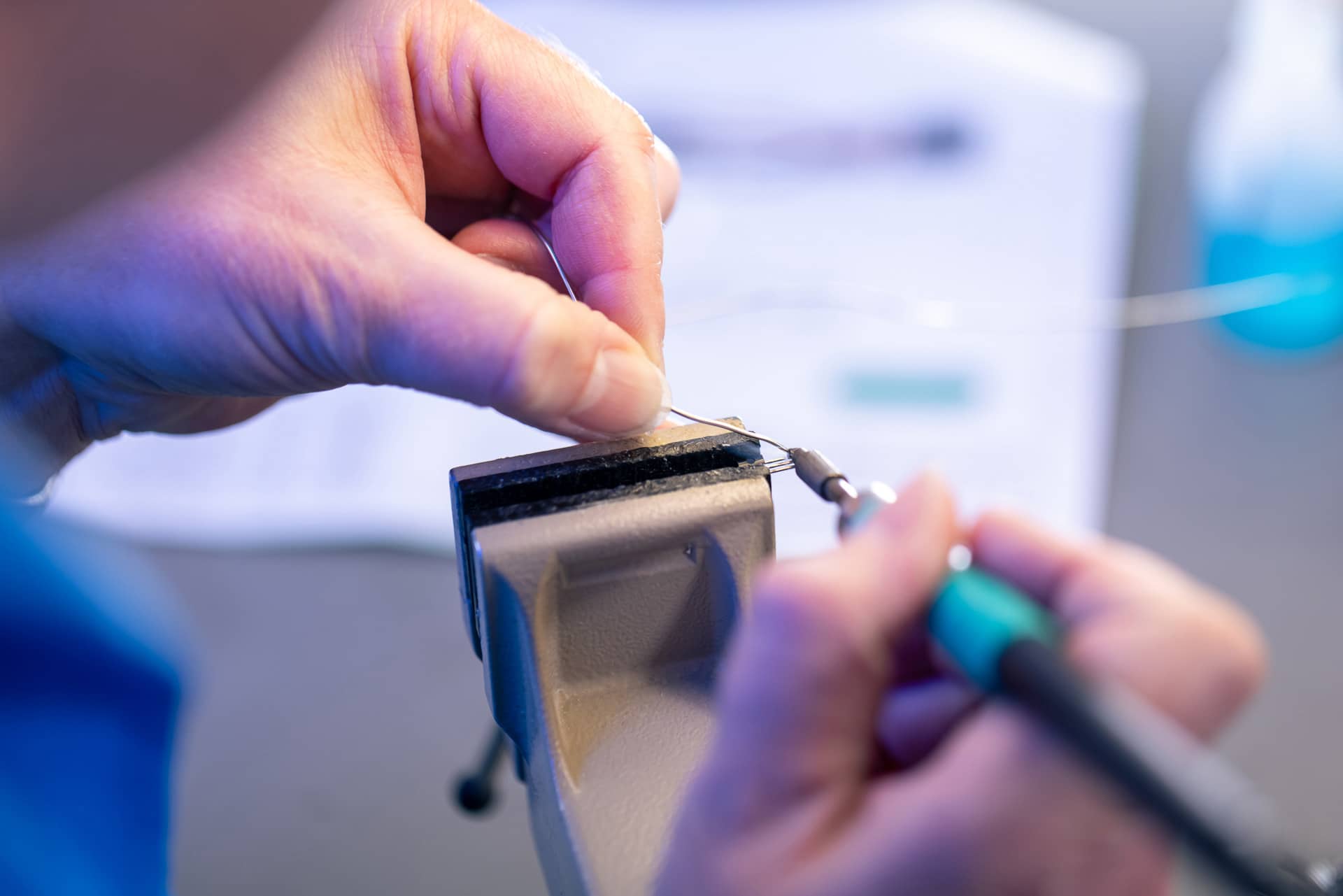
Your soldered connections are completed at rmw according to the specifications of the IPC – in consistently high quality, for which rmw’s employees are trained at least once a year. In addition to the usual connectors, electrostatically sensitive components can be processed; ESD soldering stations are available for this purpose.
Crimping
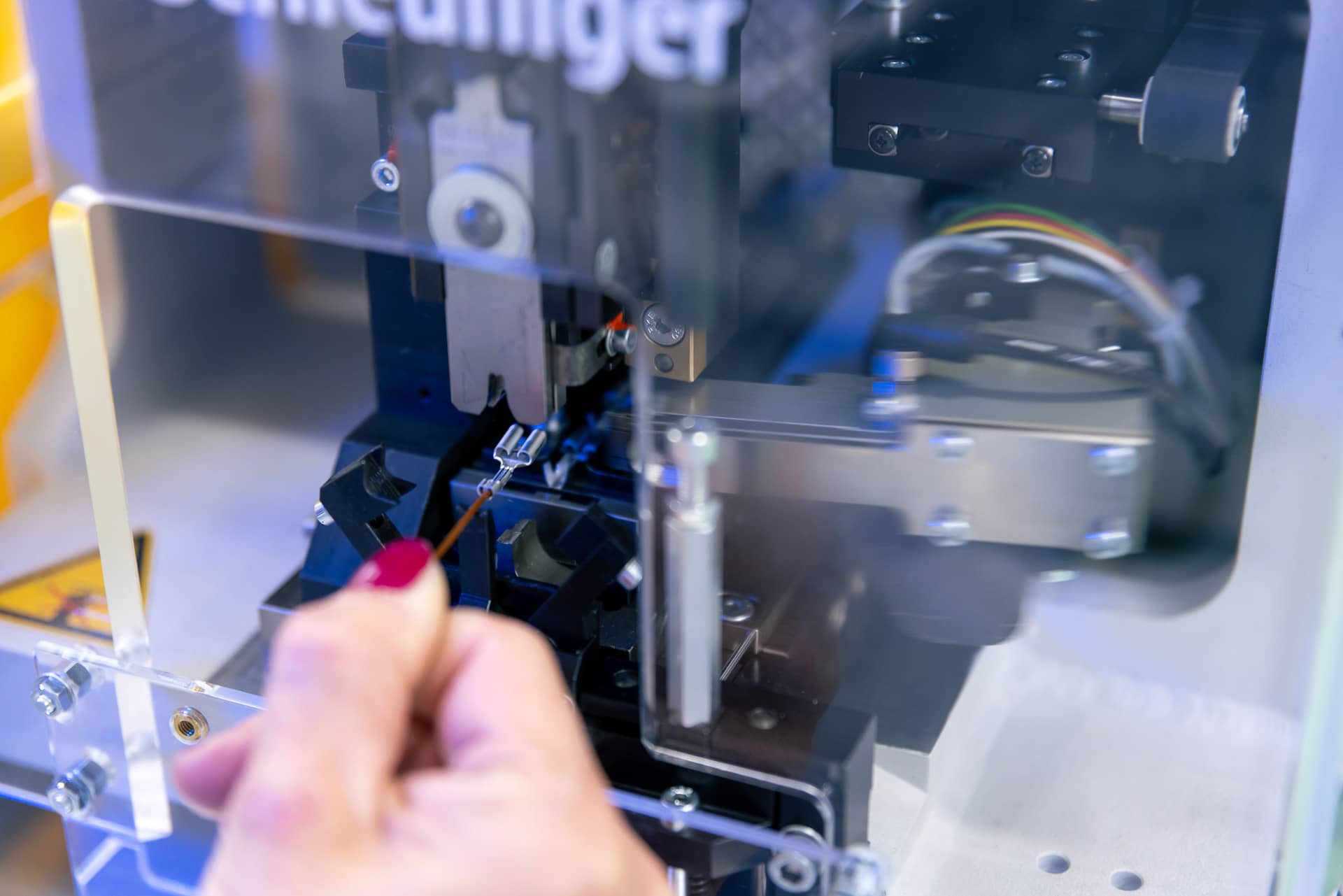
Reliable crimp connections are made at rmw by means of manual or mechanical tools, depending on the application. Thus, a wide range of possible contacts can be achieved.
- Crimping of diameters from 0.05 mm²
- up to 4 mm² (semi-automatic press)
- up to 10 mm² (manual crimper)
- up to 70 mm² (pneumatic press)
- Systematic quality monitoring via micrographs and pull-off tests
- Regular staff training
Laser-based stripping
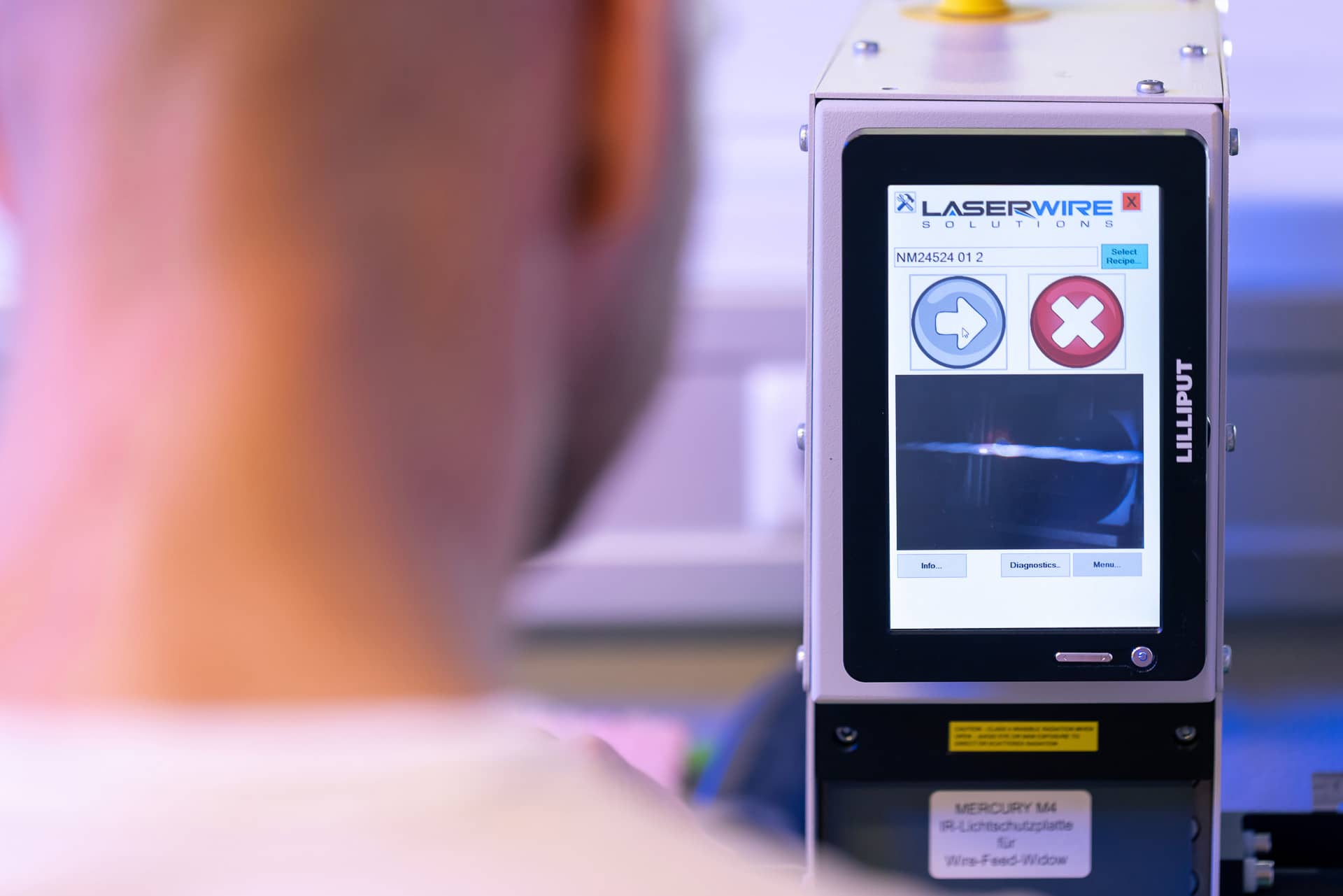
High-precision stripping of e.g., twisted shielded cables is carried out at rmw using CO2 lasers from Schleuniger or UV lasers from Laselec (SYLADE 7).
- Conductor cross-sections from 1/1000 to 16 mm² can be processed and enable a wide range of applications.
- Non-contact processing guarantees highest processing quality
- Stripping with UV laser complies with aerospace standard EN 2812
Cable marking
Depending on the application requirements, rmw uses various modern technologies to mark cables and wires for you:
Inkjet printing

Ink-jet printing in black or white on the cable sheath to achieve traceability and to print customer-specific information
Cable marking by UV laser
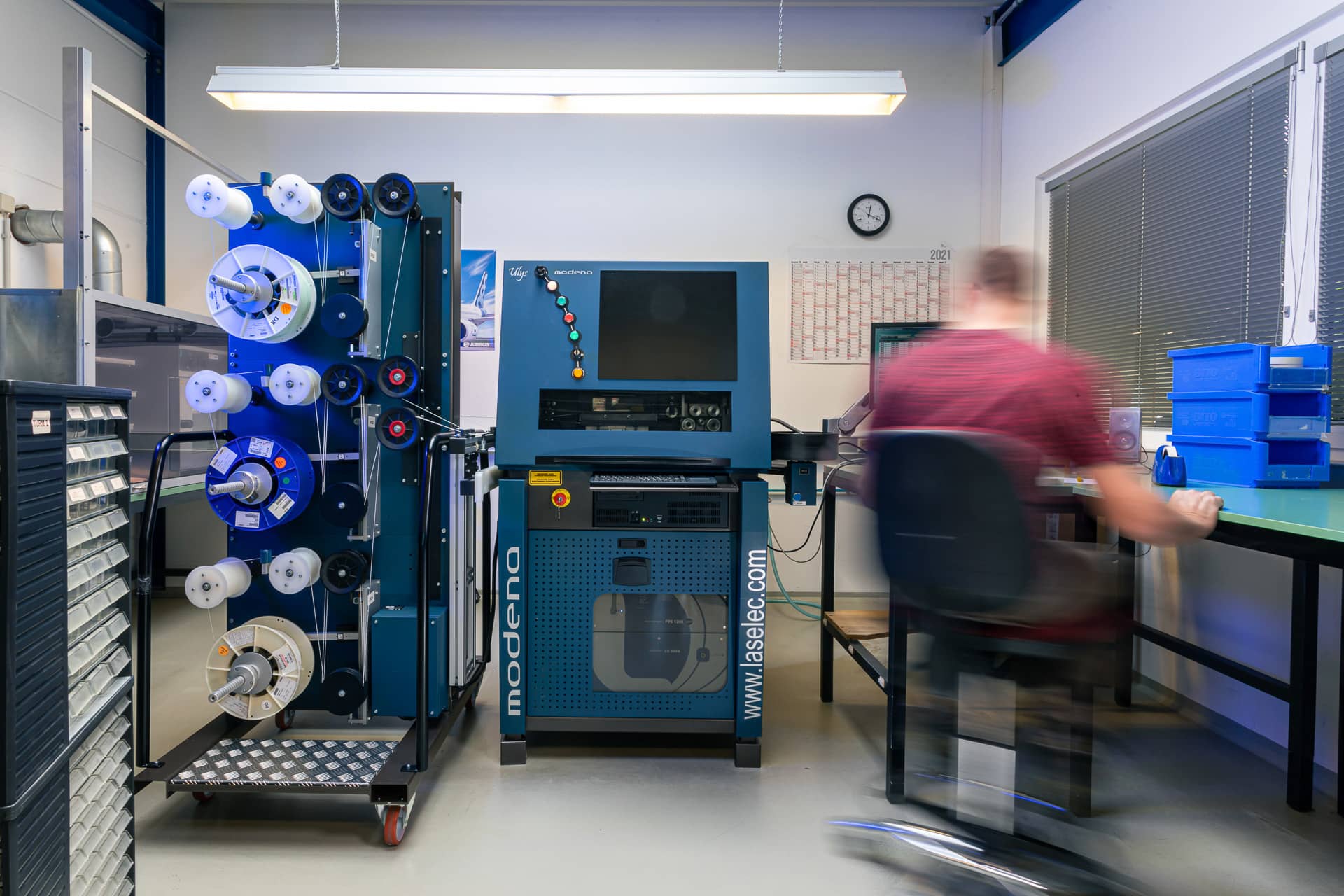
UV laser-based permanent marking of demanding aerospace cables including automated length cutting.
Thermal printing
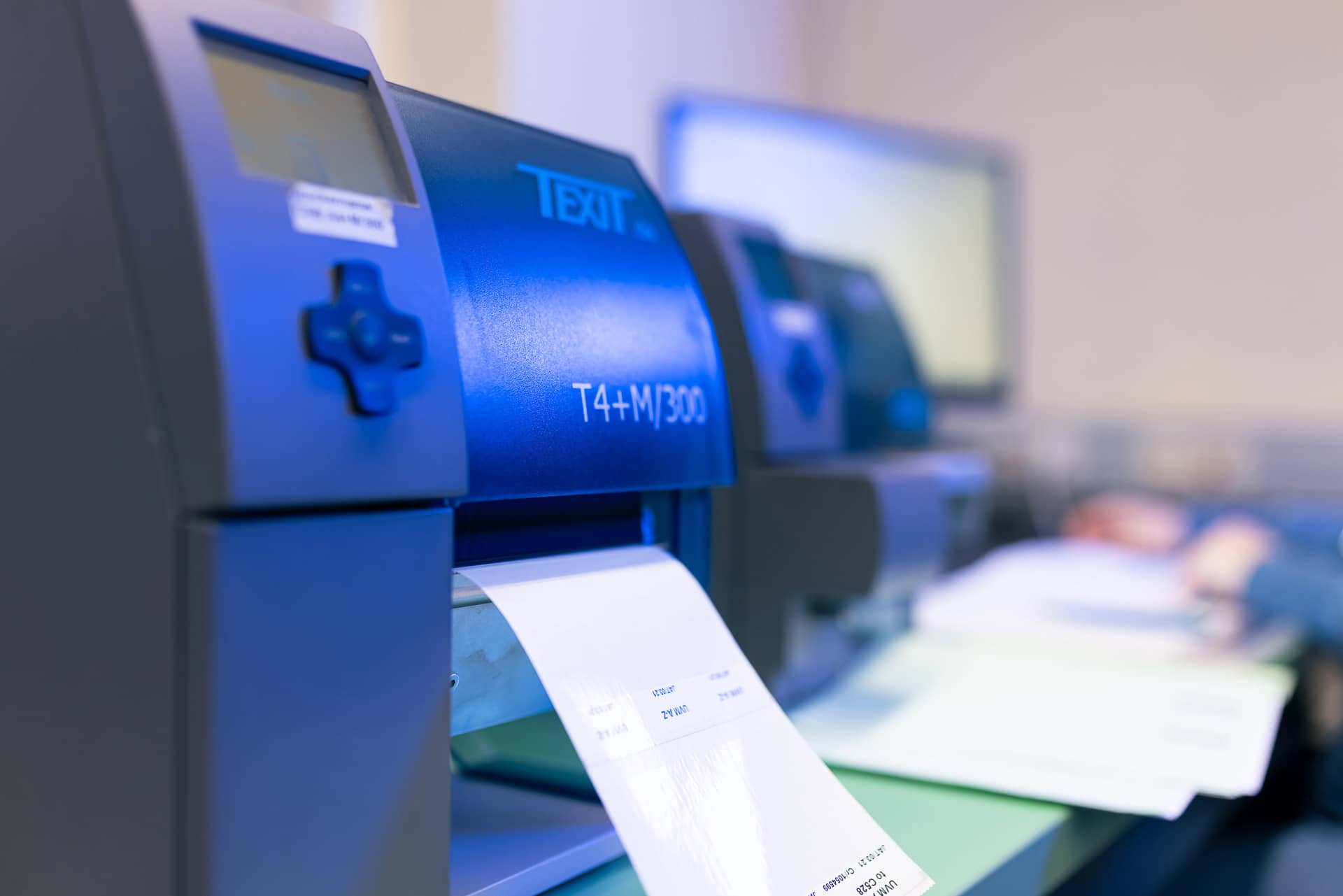
Thermal transfer & direct thermal printing for labels, identification sleeves and self-laminating labels
Shrink sleeve printing
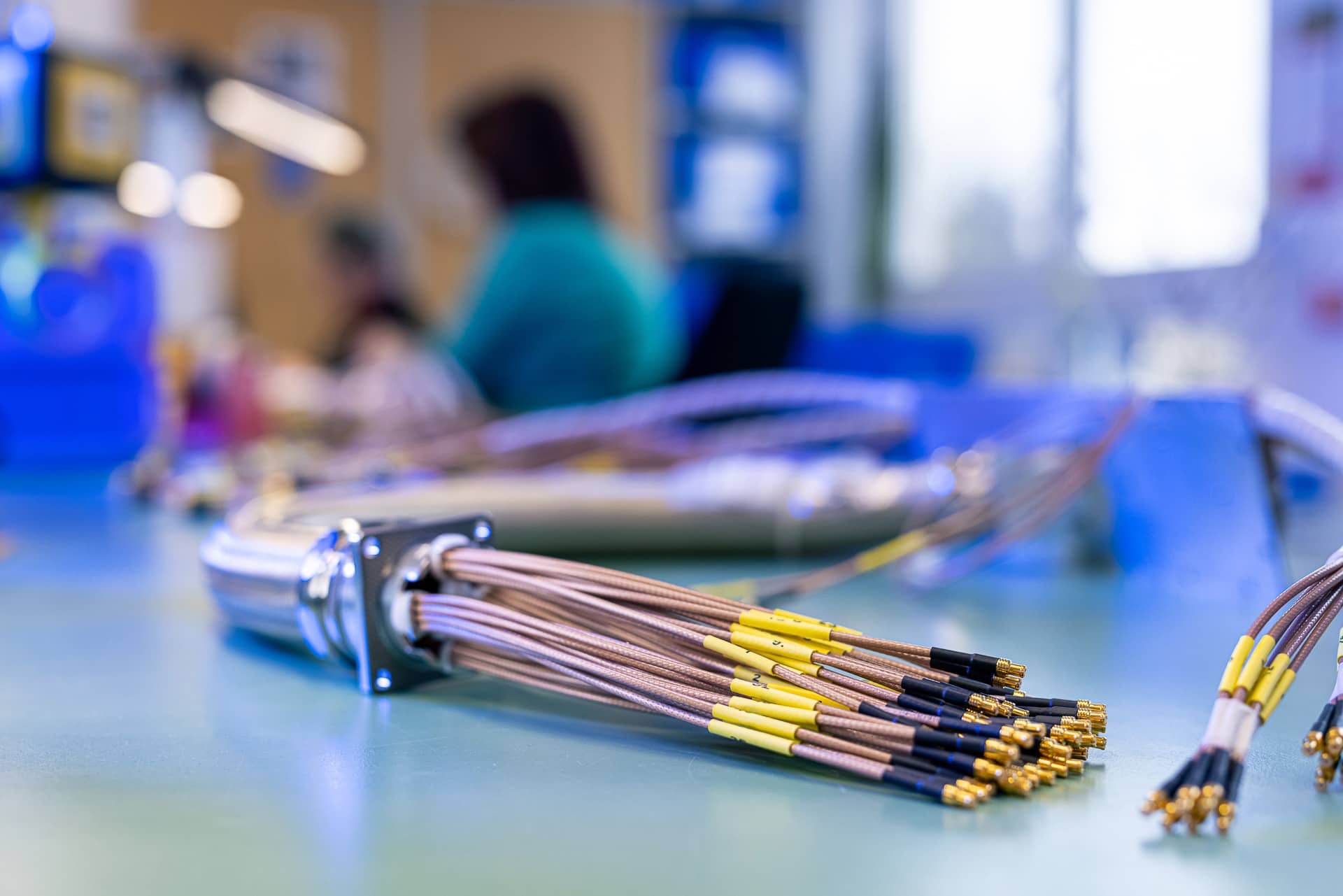
Different possibilities of individual identification by means of heat shrink printing
Testing technology for your safety
For your safety, rmw offers you 100% electrical and visual testing of all products in the high and low voltage range. For the adaptation of assembled cables, special testing equipment is built to ensure that the products function faultlessly.
The testing services of rmw include:
- Connection, short-circuit, insulation and dielectric strength tests
- Four-pole measurements
- Protective conductor tests
- Functional tests and component tests
- Customer-specific tests by arrangement
Individual test equipment
For customer-specific sub-assemblies and for 100% safety, rmw manufactures the appropriate test adapters directly in-house.
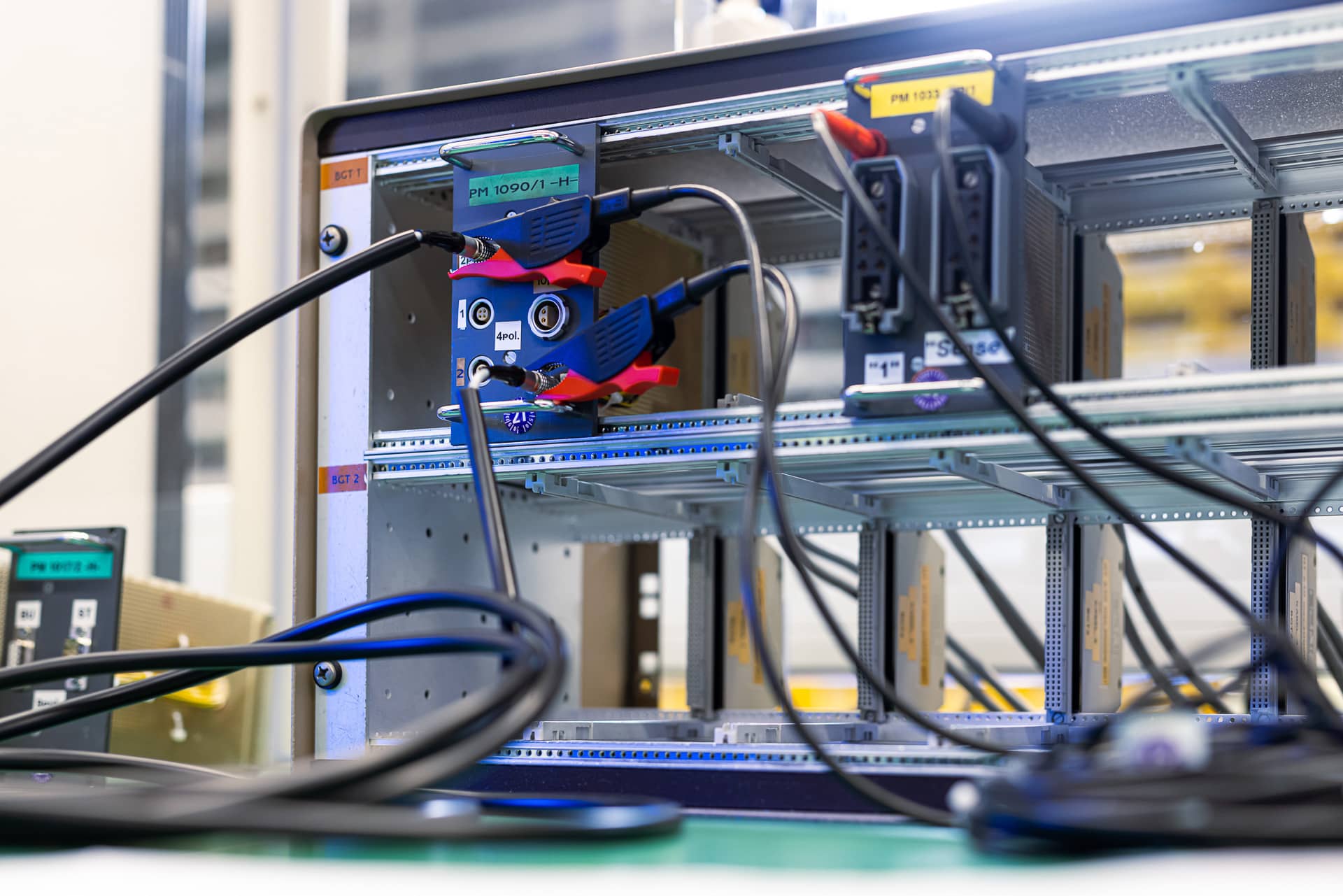
Combination tests
For increased test requirements, rmw can combine electrical tests with, for example, latching tests.
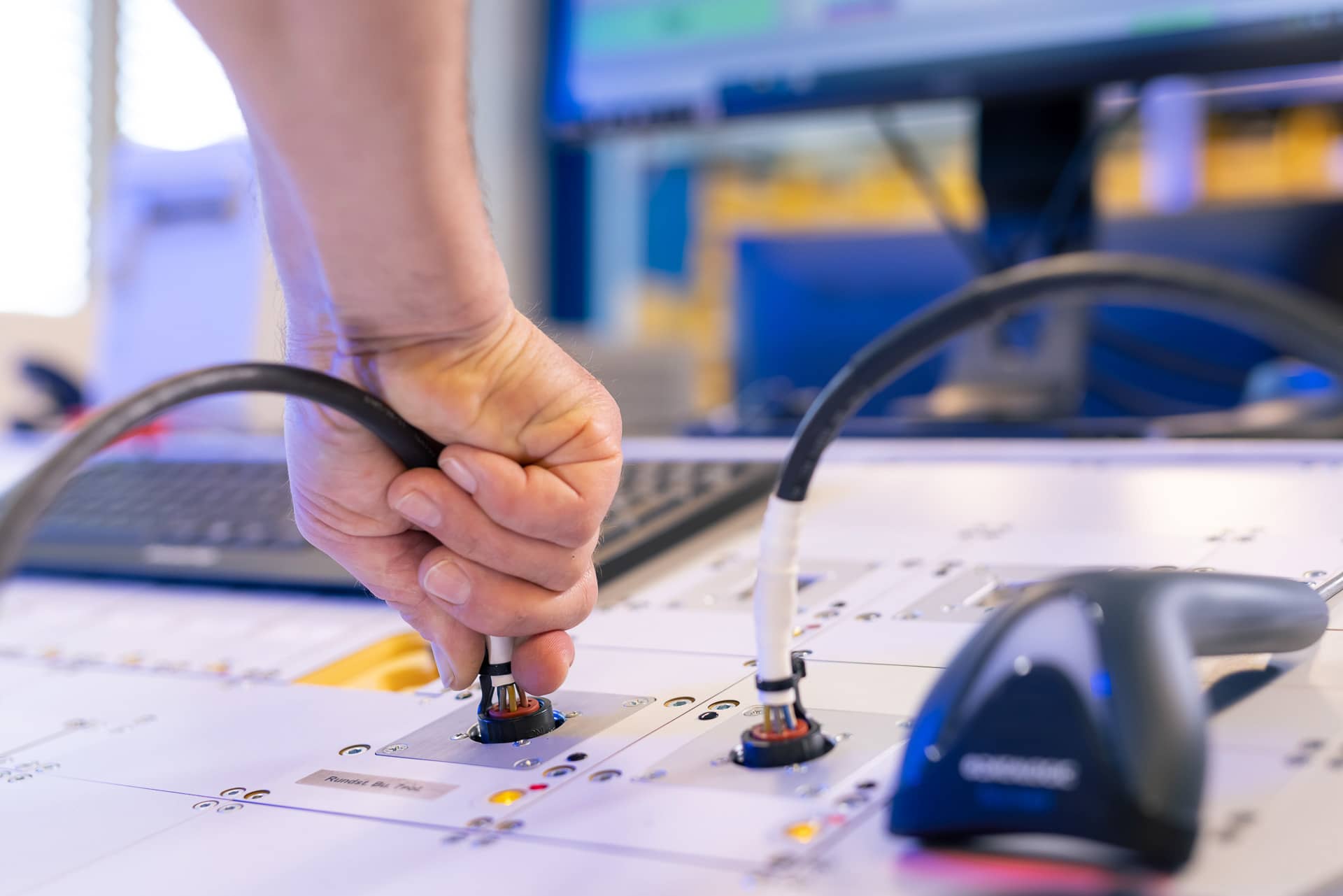
System tests
Electrical tests of sub-assemblies and complete systems incl. functional checks and comprehensive documentation of the test results.
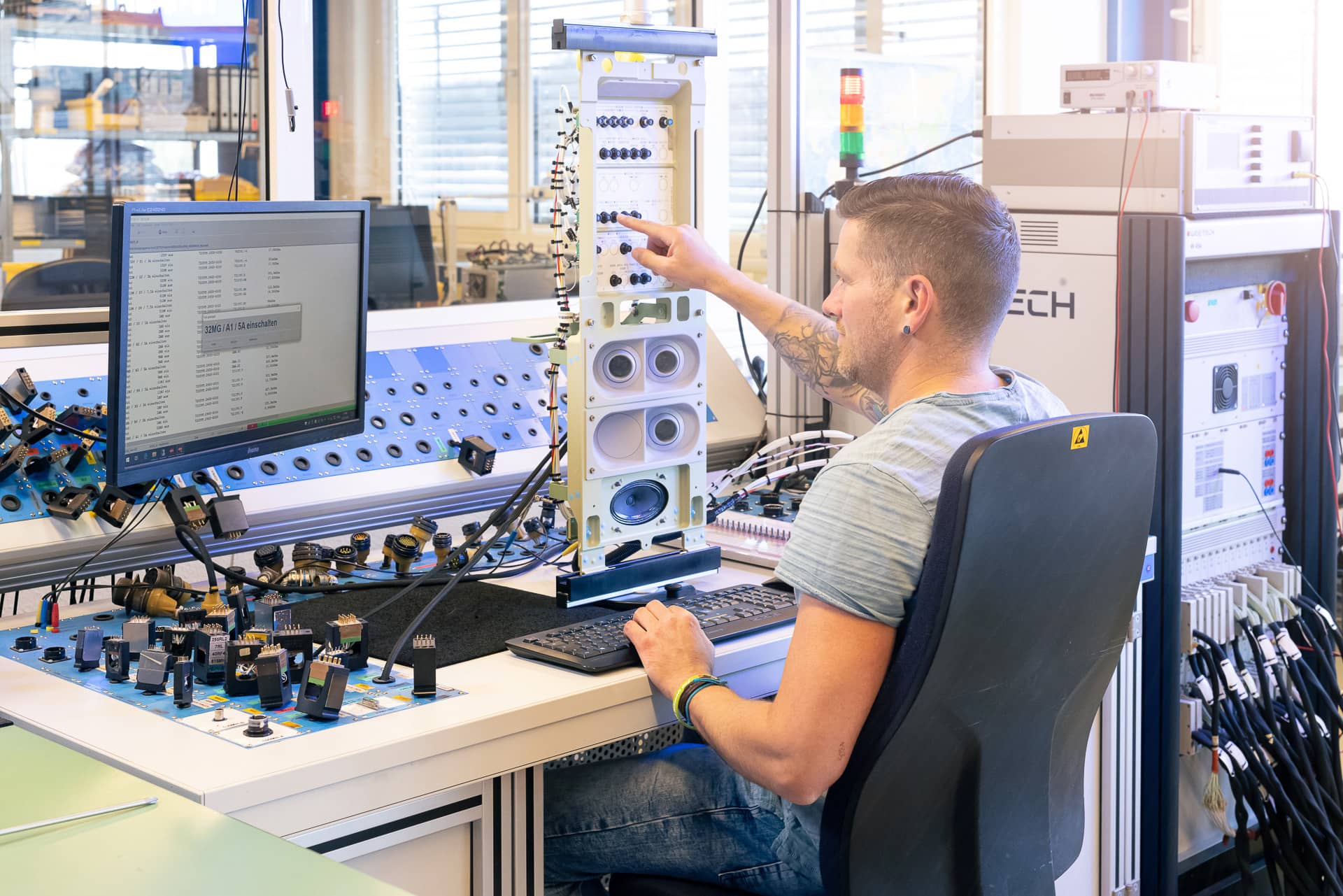
Your connection to rmw
rmw specialists are looking forward to starting something new with you. For efficient consultation, please send us the key points and technical parameters of your project in advance.
Note: By sending us your enquiry, you agree to the processing of the data you have provided for the purpose of dealing with your enquiry. Find out more about data protection here.
* Mandatory
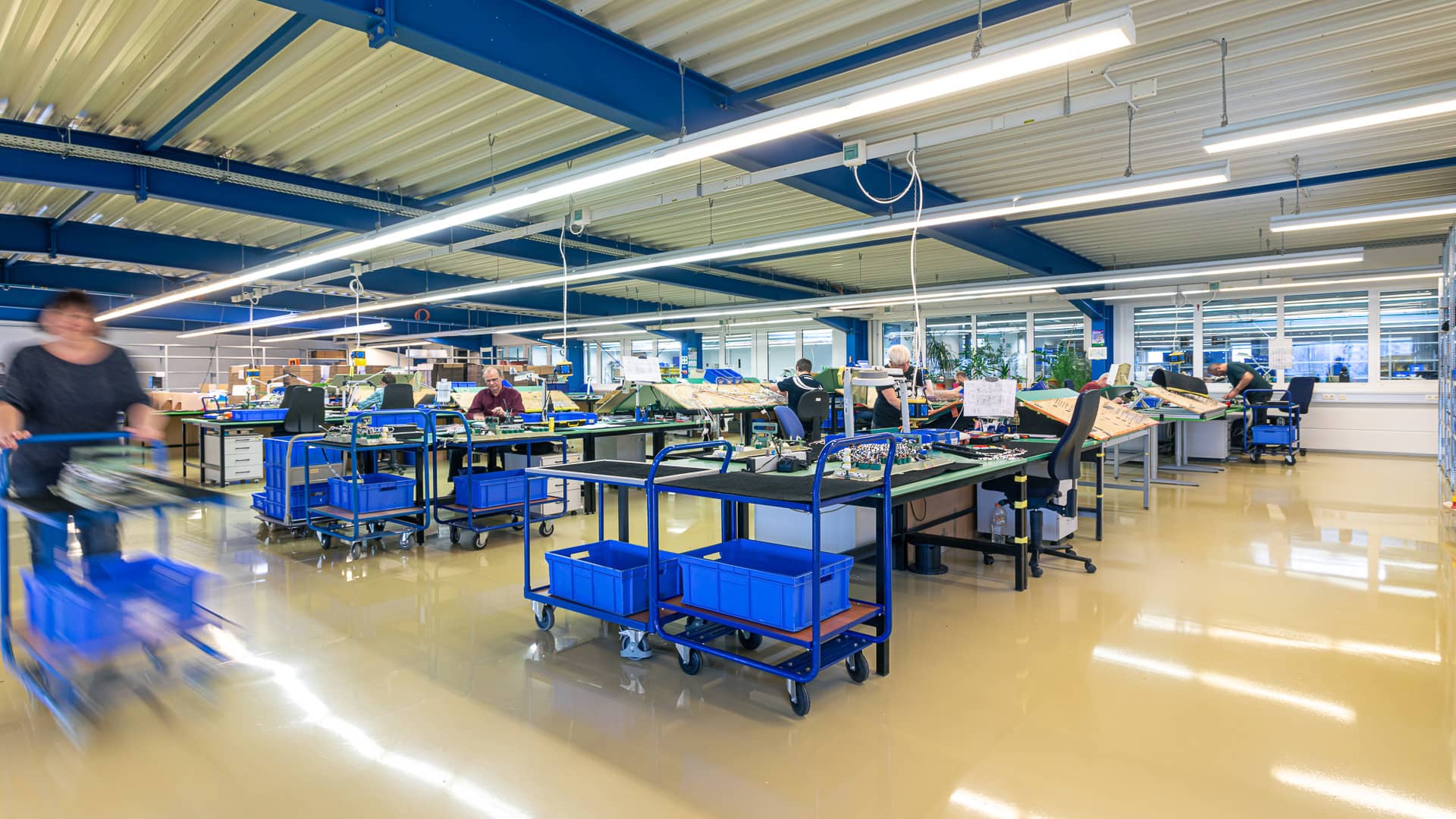
Manufacturing: High-end
On 5,000 square metres, rmw manufactures for you exactly according to your specifications – with state-of-the-art technologies, high-quality materials and decades of experience.
Personnel capacity, machinery, working and storage space, know-how and engineering standards are large enough to carry out your comprehensive, complex orders – and at the same time not too large, so that rmw is always able to react flexibly to your requirements.
FDM 3D printing
Fast, precise, cost-effective: rmw prints for you in 3D using Fused Deposition Modelling (FDM) and thus supports you in development and construction.
HotMelt
Protect sensitive electrical components or realise unconventional connector shapes: With HotMelt, rmw offers you the solution.